How Welding Inspection Madison Guarantees High Quality and Security in Fabrication
How Welding Inspection Madison Guarantees High Quality and Security in Fabrication
Blog Article
The Significance of Thorough Welding Inspection in Industrial Applications
In the realm of commercial applications, the significance of thorough welding evaluation can not be overemphasized. As we check out the diverse advantages of persistent welding assessments, one should take into consideration the broader implications on safety and security, integrity, and cost-effectiveness in industrial procedures.
Enhancing Structural Honesty
When it involves welding inspection in industrial applications, improving architectural stability is paramount. The main goal of welding assessment is to make certain that the welds can birthing the expected anxieties and lots they will certainly come across in solution. This includes an extensive examination of the welds' measurements, placement, and total high quality, guaranteeing they satisfy the defined codes and requirements. Precise evaluation techniques, such as visual evaluation, ultrasonic testing, and radiographic testing, are vital in identifying issues that can endanger the framework's safety and security and capability - Welding Inspection Madison.
The value of preserving architectural stability in welded frameworks can not be overstated. Poorly implemented welds can lead to catastrophic failings, causing expensive repair services, downtime, and also endangerment of human lives. Consequently, examiners play an essential duty in the lifecycle of commercial components, offering assurance that the welding process supplies the preferred strength and sturdiness.
Furthermore, progressed technologies, such as phased selection ultrasonic testing and electronic radiography, offer boosted capabilities in identifying potential weak points, enabling rehabilitative steps prior to problems rise. By prioritizing the stability of welds via meticulous examination, industries can guarantee functional efficiency and extend the durability of their framework.
Identifying Welding Flaws
Recognizing welding defects is a critical aspect of making certain the safety and dependability of welded frameworks. These issues can jeopardize the honesty of the entire assembly and, if left unaddressed, may result in disastrous failings. Typical welding defects include porosity, cracks, incomplete combination, and damaging. Each of these defects develops from certain reasons, such as inappropriate welding strategies, contamination, or poor warmth control.
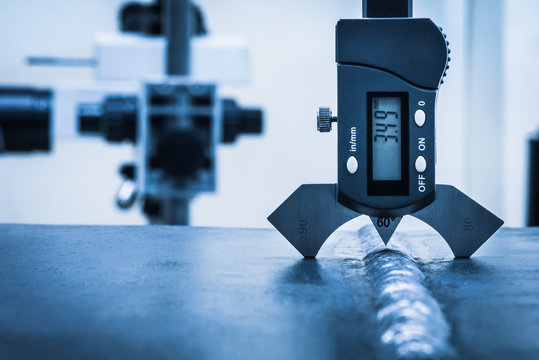
Proficient inspectors use both aesthetic evaluation and progressed non-destructive testing (NDT) approaches, such as ultrasonic or radiographic testing, to identify these problems. The prompt recognition and rectification of welding flaws are necessary to maintain the architectural honesty and longevity of industrial parts.
Making Sure Conformity Criteria
Conformity with well established requirements, such as those supplied by the American Welding Society (AWS) and the International Organization for Standardization (ISO), guarantees that welds satisfy minimal security and quality requirements. These criteria incorporate a large variety of requirements, consisting of material specifications, welding treatments, and credentials of welders.
Routine audits and evaluations are important in validating compliance. Inspectors need to possess a comprehensive understanding of the pertinent requirements and be experienced at utilizing numerous non-destructive testing (NDT) methods to assess weld quality. By ensuring that welding methods align with compliance requirements, firms reduce the threat of non-conformity, which can bring about lawful obligations and security risks.
Additionally, preserving conformity not only safeguards architectural stability yet likewise boosts a company's online reputation in the market. Stakeholders and clients are most likely to trust fund firms our website that constantly show a dedication to quality and security via rigorous compliance. Therefore, guaranteeing conformity requirements is an essential part in the effective application of welding in industrial applications.
Minimizing Maintenance Prices
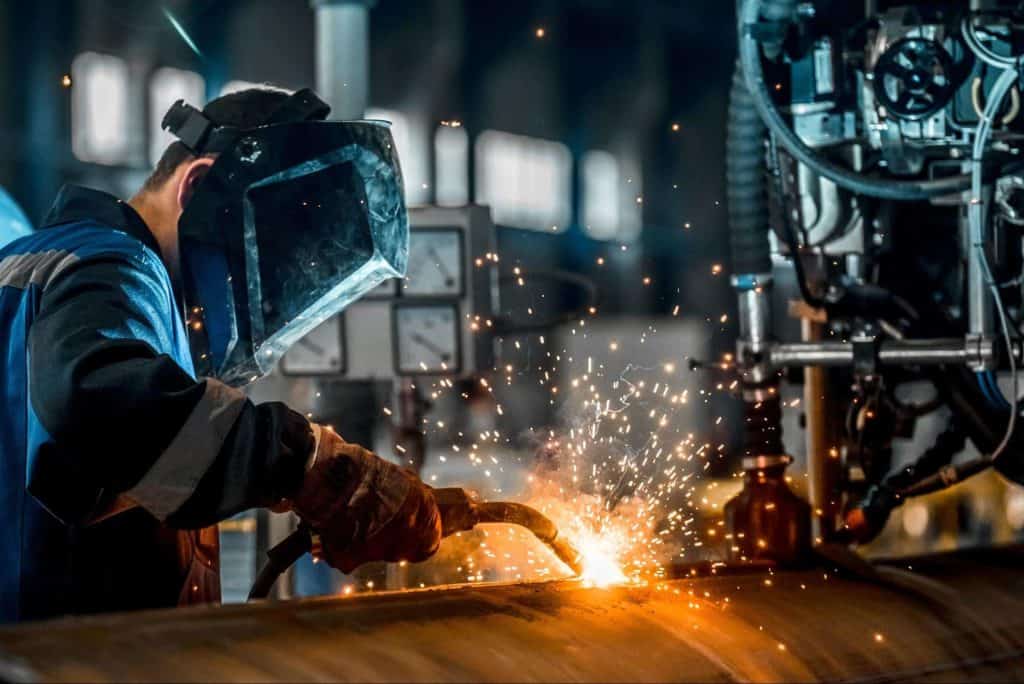
The application of advanced non-destructive testing (NDT) techniques, consisting of ultrasonic, radiographic, and magnetic fragment evaluations, enhances the capability to discover subsurface defects without endangering the architectural stability of components. By using these methods, sectors can substantially extend the service life of their equipment, lowering downtime and the associated economic concern of maintenance activities.
Furthermore, a durable welding assessment regime sustains the optimization of upkeep schedules, shifting from responsive to predictive upkeep strategies. This positive strategy not only cuts unforeseen failings but likewise simplifies resource appropriation, guaranteeing that upkeep efforts are concentrated and reliable. Ultimately, the financial investment in strenuous welding evaluation is countered by the substantial financial savings recognized with lowered maintenance needs, adding favorably to the total functional performance of industrial business.
Improving Precaution
Although safety is an extremely important concern in industrial operations, accomplishing ideal safety and security standards calls for a devoted concentrate on the top quality and integrity of bonded structures. Welding assessment plays an important function in this context, as it makes certain that all connections and joints meet strict safety and security criteria. Comprehensive inspections aid identify problems such as cracks, porosity, or incomplete fusion that could compromise architectural integrity. Such issues, if left unaddressed, pose substantial dangers, potentially causing tragic failings.
To boost precaution, taking on sophisticated non-destructive testing (NDT) techniques is important. Approaches like ultrasonic screening, radiographic screening, and magnetic bit evaluation allow for detailed exam without damaging the structure. These modern technologies allow assessors to discover hidden imperfections early in the building process, promoting timely rehabilitative actions. Carrying out a robust high quality control system that includes routine training for assessors and welders makes certain adherence to established safety and security requirements.
Finally, cultivating a culture of security within the company stresses the importance of complete welding evaluations. Urging open communication and partnership amongst engineers, welders, and inspectors adds to a shared dedication to security quality. Welding Inspection Madison. In doing so, sectors can safeguard their operations, company website safeguard employees, and keep public trust

Final Thought
Detailed welding examination is essential in industrial applications, considerably enhancing structural integrity and reliability. By using innovative non-destructive screening techniques, potential welding defects such as cracks and incomplete combination are determined early, making sure conformity with market standards and cultivating customer depend on. Rigorous inspections bring about minimized maintenance costs and add to a safer working atmosphere. Ultimately, the persistent implementation of welding assessments plays a crucial duty in keeping operational performance and security in industrial setups.
As we check out the multifaceted advantages of thorough welding examinations, one need to consider the more comprehensive implications on safety and security, reliability, and cost-effectiveness in industrial operations.
The key goal of welding assessment is to make certain that the welds are qualified of birthing the expected loads and stress and anxieties they will certainly run into in solution. Reliable welding evaluation plays an integral role in lessening these prices by ensuring the stability and long life of welds, therefore mitigating the risk of premature failures.Thorough welding inspection is essential in industrial applications, considerably improving architectural stability and dependability. Inevitably, the thorough implementation of welding examinations plays an essential function in preserving operational efficiency and safety in industrial settings.
Report this page